FULL STORY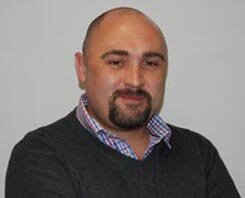
While 3D printing has captivated the imagination of the general public, similarly exciting developments are emerging from the world of inkjet printing. Or, to be more specific, from the world of jet printing; when the ink is removed and other materials introduced, it becomes possible to print a wide range of outputs.
Thats according to Charl Vogel, national sales manager, Xerox production systems group direct, Bytes Document Solutions (pictured right). He says Drop on Demand (DoD) technology in Impika printers allows these machines to print electronic circuit boards and other components, apply nano-particles for RFID tracing, special varnishes for security purposes, decorative finishings, and more. The secret to material jet, or matjet printing lies in digital DoD piezoelectric jet technology, Vogel commented.
Impika is a specialist manufacturer of jet printing devices which was recently acquired by Xerox.
Jet printing is a contactless process which means it is capable of placing substrate on a wide variety of materials, such as paper, ceramics, glass, textiles and plastics, both flat and embossed. The more familiar consumable which is put through jet printers is ink but new developments mean other materials can now also be used.
Vogel explained the two main types of jet printing in the familiar context of inkjets. Continuous inkjet uses a continuous flow of ink that is deviated to create the pattern to be printed. That contrasts with DoD, which applies a principle of creating a droplet only when necessary, rather than constantly.
With DoD, the droplets are ejected in various ways including piezoelectric, thermal, valve jet and thermofusion. Uniquely, piezoelectric DoD inkjet technology creates droplets by mechanical deformation; this differs from thermal DoD for example, where droplets are generated by raising the temperature.
Piezoelectric printheads digitally project micro drops of ink or other material (a few picolitres a picolitre is one millionth of a microlitre, which itself is a millionth of a litre) through nozzles producing images directly on the substrate. This contrasts with traditional printing where a series of time and money consuming stages are required before printing a new image, such as a screen for silkscreen printing, a plate for offset, an engraving cylinder for flexography, or a pad for pad printing, explained Vogel.
This flexibility means piezoelectric DoD can be applied in customised printing, as the jets can create a new image at each print. One of the main advantages of piezoelectric technology is that it can cope with different types of ink and other materials. It can print UV, solvent, water-based and hot melt ink, with a larger range of viscosity than a thermal inkjet can handle. It also works with conducting materials so it can print specialised output like RFID labels and printed circuits at highly competitive costs and with reduced pollution, Vogel continued.
Additional special fluids deposit solutions include decorative printing on finished goods, and serial numbers and other identifying marks on microelectronics and biomedical products. Just like 3D is pushing the boundaries of what is possible in the printing market, jet technology is also broadening the scope of the output which can be produced from a printer. Its an exciting emerging field where the possibilities are only now being explored, Vogel concluded.
© Graphic Repro On-line, 13 November 2014.
|