FULL STORY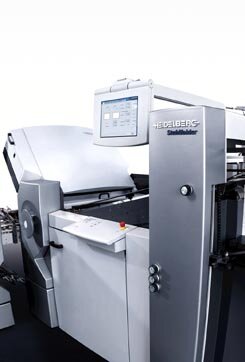
Continuous quality check by using the same barcode system for all units
High flexibility and production variety for both, digitally and conventionally printed jobs
At the Hunkeler Innovation Days taking place in Lucerne, Switzerland from 23 to 26 February, 2015, Heidelberg will show solutions for the production of digitally printed softcover brochures of high quality on stand B02.
The TH 56 Stahlfolder of Heidelberg co-operates seamlessly as inline folder with the modules of Hunkeler. The machine folds sheets which are unwound from a reel digitally printed by Ricoh and cross cut in one workstep
Themed HEI Flexibility this is an answer to the trend to smaller runs and to flexibility as high as possible with the finishing of digitally and conventionally printed jobs.
Together with its partners Hunkeler, ATS, Müller Martini, and Polar, Heidelberg will show a flexible machine network where a complete brochure is produced live. This brochure consists of a content which was digitally produced in rotary printing and a cover which is bound by means of hotmelt glue, finally getting a three-side trim in one work step. With this configuration the continuous control of contents and cover per barcode is shown. All units involved use the same barcode system in order to make sure that the product is compiled and produced correctly.
The systems consists of a Hunkeler UW6-unwinding module, the following cross cutter CS6-I and the directly connected Heidelberg Inline folder Stahlfolder TH 56, folding the sheets and transferring them as collected pile to an ATS bundler FAB A 820. By means of the barcode it is ensured that every set has been collated completely in the bundler. Afterwards the folded signatures are brought together with the cover on the latest Müller Martini perfect binder and bound to a completed brochure. The Müller Martini perfect binder represents a world premiere which is shown to the trade experts at the Hunkeler Innovation Days for the first time. Here, the barcode ensures as well that cover and contents fit together. The final three-side trim is done automatically in the POLAR three-side trimmer BC-330, where the production barcode is read again.
High flexibility and production variety for both, digitally and conventionally printed jobs
The solution shown allows for the production of a large variety of products in small runs without having to do elaborate retrofitting. It is also possible to process both, digitally printed and conventionally printed jobs according to requirements.
Heidelberg and Hunkeler have worked together as partners for integrated finishing solutions in digital printing for several years. The Stahlfolder folding units of Heidelberg are used in many Hunkeler installations worldwide, both in rotary printing, as well as in digital sheetfed printing.
© Graphic Repro On-line, 29 January 2015.
|